The RHODaS project is driving innovation in heavy-duty electric transport by integrating advanced digital twin technology into the design and operation of next-generation powertrains. This approach enhances the development, monitoring, and predictive maintenance of key components—offering a significant leap forward in efficiency, reliability, and sustainability.
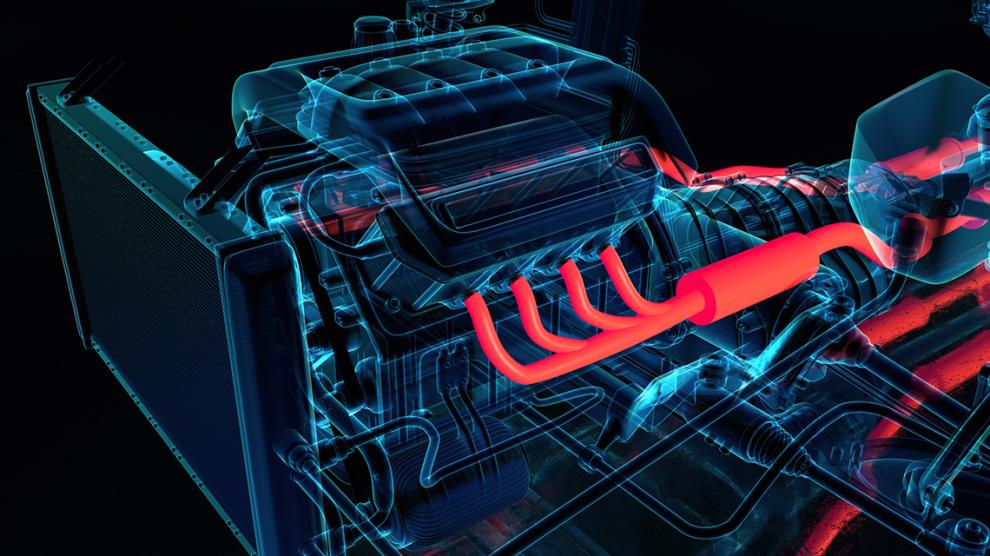
A Holistic Digital Twin Framework
The RHODaS project´s latest report, “Definition and Implementation of a Holistic Digital Twin of the Integrated Motor Drive,” marks a major milestone in the project. It outlines the creation of detailed virtual replicas—or digital twins—of three essential subsystems: the inverter, e-motor, and gearbox. These models simulate real-world performance, enabling engineers to predict failures, optimise system behaviour, and reduce reliance on physical prototypes.
Subsystem Modelling and Integration
Each digital twin captures the thermal and electro-mechanical dynamics of its respective component:
- The inverter model simulates the electro-thermal behaviour of wide bandgap (WBG) devices such as Gallium Nitride (GaN) and Silicon Carbide (SiC) switches, with data-driven interpolation to estimate power losses based on experimental results.
- The e-motor twin applies a thermal equivalent circuit to model heat transfer between the rotor and stator, predicting temperature changes over time.
- The gearbox model uses 3D interpolation techniques to estimate oil temperature and surface heat dissipation based on operating parameters such as torque, shaft speed, and ambient conditions.
These digital twins are developed by Aarhus University (AU) using MATLAB/Simulink and C++ and are seamlessly integrated into the RHODaS cloud platform. This enables both real-time monitoring and offline analysis, supporting scalability and system-level adaptability.
Performance Analysis and Predictive Capabilities
Extensive sensitivity analyses were performed to assess the thermal response of the subsystems under varying conditions—such as changes in switching frequency, torque, and ambient temperature. These insights help define operational limits and identify opportunities for performance optimisation.
One of the standout innovations is the inverter’s use of interpolation-based modelling, ensuring accurate power loss estimation. Meanwhile, the e-motor and gearbox models contribute valuable predictive insights into component longevity and efficiency, essential for reliable heavy-duty electric vehicle operation.
Enabling Intelligent, Sustainable Mobility
By bridging the gap between physical hardware and virtual simulation, RHODaS is laying the groundwork for intelligent diagnostics, advanced monitoring, and predictive maintenance. This approach reduces downtime, enhances component lifespan, and supports resource-efficient engineering practices.
Looking ahead, the tools and methodologies developed in RHODaS will enable system-level co-simulation and control strategies, further enhancing powertrain adaptability and performance. The modular design of the digital twin architecture ensures its compatibility with future technologies and evolving system requirements.
Conclusion
The RHODaS project exemplifies the transformative impact of digital twin technology in the development of high-performance electric powertrains. By enabling data-driven decision-making, performance optimisation, and predictive reliability, RHODaS is helping to shape the future of sustainable electric mobility. As the project progresses, it will continue to deliver innovations that strengthen Europe's leadership in clean, intelligent transport solutions.
Download the full report here > RHODaS 4.3. efinition ImplementationHolistic Digital Twin IMD