The RHODaS project is delivering transformative innovations in heavy-duty electric mobility. A key aspect of this evolution is the RHODaS IoT platform—a robust, cloud-based system designed to elevate the performance, reliability, and sustainability of connected trucks.
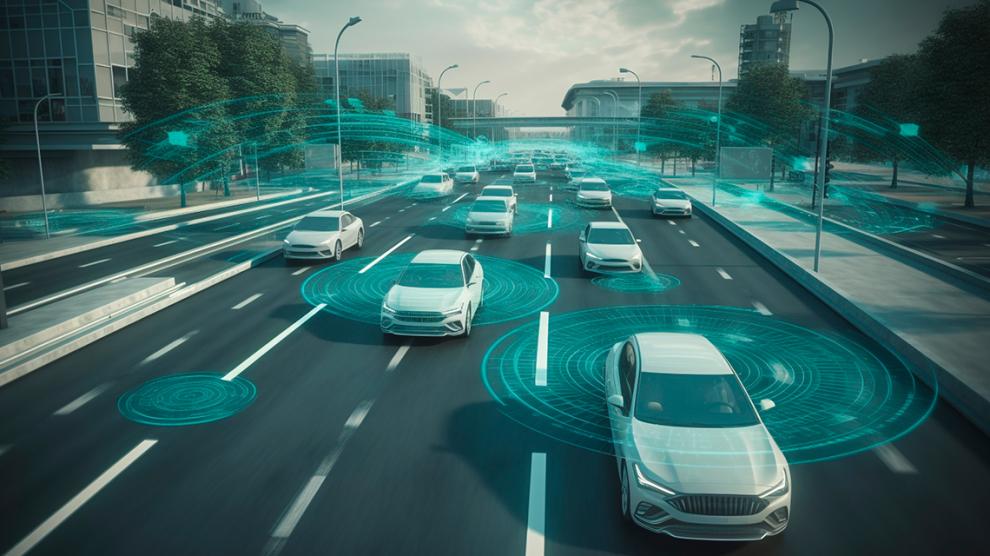
The platform incorporates cutting-edge technologies such as Digital Twins, Decision Support Systems (DSS), and real-time monitoring tools—enabling advanced diagnostics, predictive maintenance, and adaptive control strategies.
Digital Twins and Decision Support Systems
At the heart of the RHODaS IoT platform is a suite of Digital Twins, representing key powertrain components such as the inverter, electric motor, and gearbox. These virtual models operate in dual modes—as predictive simulators and real-time execution engines—allowing engineers to simulate system behaviour, analyse live data, and forecast failures before they occur.
Complementing the digital twins is the Decision Support System, which combines AI models, historical trend data, and real-time fault flags to deliver actionable insights. This module supports critical decisions related to fault detection, condition-based maintenance, and operational optimisation.
Key Modules for Monitoring and Lifecycle Management
The IoT platform also includes three additional core modules:
- Online Monitoring – Provides live tracking of key operational parameters.
- Key Performance Indicators (KPIs) – Deliver measurable metrics to assess system efficiency and reliability.
- Digital Vehicle Passport (DVP) – Maintains a complete digital record of the vehicle’s lifecycle, supporting fleet management and sustainability tracking.
These modules are connected via Azure Functions middleware, which enables seamless data communication and synchronised execution across the entire platform.
Rigorous Testing and Validation
To ensure robustness and reliability, the RHODaS IoT platform underwent a hierarchical testing strategy, beginning with unit tests of individual modules and advancing through integration and system-level validation. Testing involved synthetic datasets simulating real-world scenarios such as variable torque, thermal fluctuations, and mechanical stress.
Nine key use cases were tested, covering everything from real-time diagnostics to sustainability assessments. Highlights include:
- The Digital Twin module accurately predicted power losses and component temperatures.
- The DSS successfully identified faults and proposed corrective actions.
- The KPI module quantified system efficiency and operational reliability.
Next Phase: Integration with Physical Hardware
With this validation phase completed, the RHODaS IoT platform is now ready for full system integration with physical hardware. This next step will assess performance in operational environments, ensuring scalability, responsiveness, and long-term durability under real-world conditions.
Conclusion
The RHODaS IoT platform represents a milestone in connected vehicle innovation, offering a modular, intelligent architecture for the future of electric heavy-duty transport. By bridging cloud-based intelligence with real-time monitoring and digital twin technology, the platform lays a strong foundation for a new era of predictive, efficient, and sustainable mobility.
As RHODaS moves towards real-world deployment, its contributions will position the project at the forefront of Europe’s transition to smart, clean, and connected transport systems.