RHODaS researchers from Valeo have submitted two reports that provide a comprehensive overview of the specifications and architecture for the Integrated Motor Drive (IMD) prototype, and aim at defining the performance metrics, use cases, and an initial set of automotive standards.
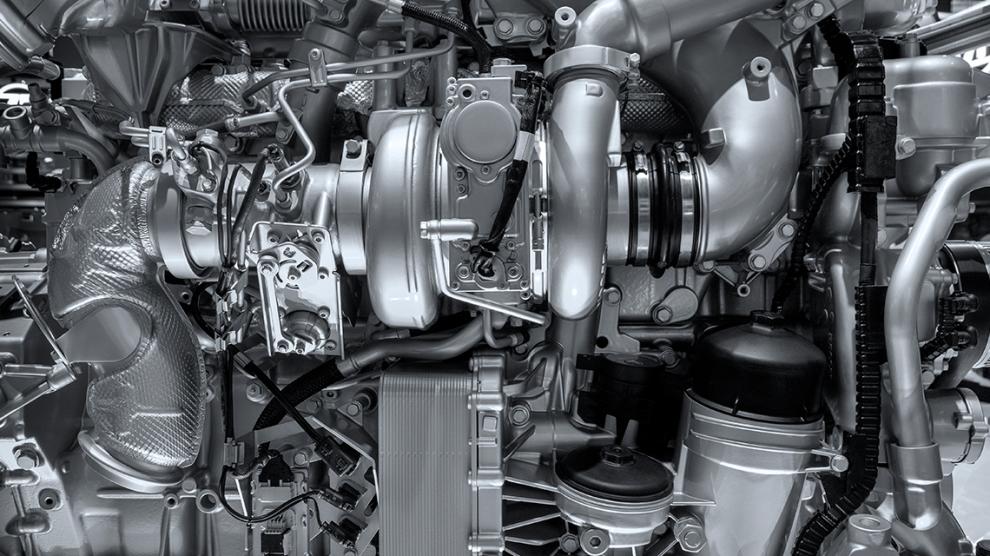
The core components of the IMD, including the power converter, thermal management system, and gearbox, are detailed, along with their interfaces and associated sub-parts. The power converter, integral to the IMD powertrain, interfaces with other critical sub-components like the thermal management system and digital twin platform. Hardware interfaces for the electric engine, gearbox, and software interfaces such as the Internet of Things (IoT) Gateway are also outlined.
Moreover, the report underscores the significance of software in driving the IMD, dispersed across multiple control units. The Thermal Control Unit (TCU) ensures optimal cooling of the power converter under normal conditions whilst also regulating output and temperature during abnormal scenarios. The Electronic Control Unit (ECU) governs the power converter and electric motor, orchestrating the IMD's output in terms of speed and torque by converter switching. Additionally, a data acquisition system is in place to measure and monitor IMD parameters during operation and tests, supported by various sensors.
To enhance functionality and implement crucial ancillary functions like condition monitoring for averting significant powertrain failures, a cloud platform aggregates and stores data from the powertrain. This platform encompasses an IoT platform, Digital Twin platform, and a Gateway, enabling seamless data collection and storage for further analysis and improvements. The ultimate aim is to facilitate a robust and efficient IMD through meticulous hardware and software designs, ensuring its successful integration and performance in the envisioned powertrain.
Testing and performance evaluation of the Integrated Motor Drive (IMD) will be undertaken by the Bosmal Automotive Research and Development Institute in RHODaS Work Package 5. The initial focus has been on outlining the subcomponents of the IMD, and then defining the performance metrics, use cases, and an initial set of automotive standards.
By aligning with vehicle target requirements, the performance parameters of the subcomponents are determined and serve as the basis for establishing test bench requirements, and the necessary equipment like dynos, pumps, chillers, etc. Moreover, the report emphasises studying use case scenarios to create a linkage between typical driver use cases and IMD-level use cases, essential for defining comprehensive testing procedures and where target performances for the IMD are established based on inverter output.
Preliminary requirements for the test bench have been defined to assess IMD performance, and the hardware and capabilities for the test bench will be solidified through coordination with other RHODaS partners. Finally, the report identifies various use cases that will help shape the procedures for testing the key operational functionalities of the IMD.