The RHODaS project continues to make major strides in the development of advanced power electronics for sustainable transport. Our latest report provides insights into the design, integration, and validation of Universitat Politècnica de Catalunya´s hybrid T-Type power converter prototype engineered for heavy-duty electric vehicles.
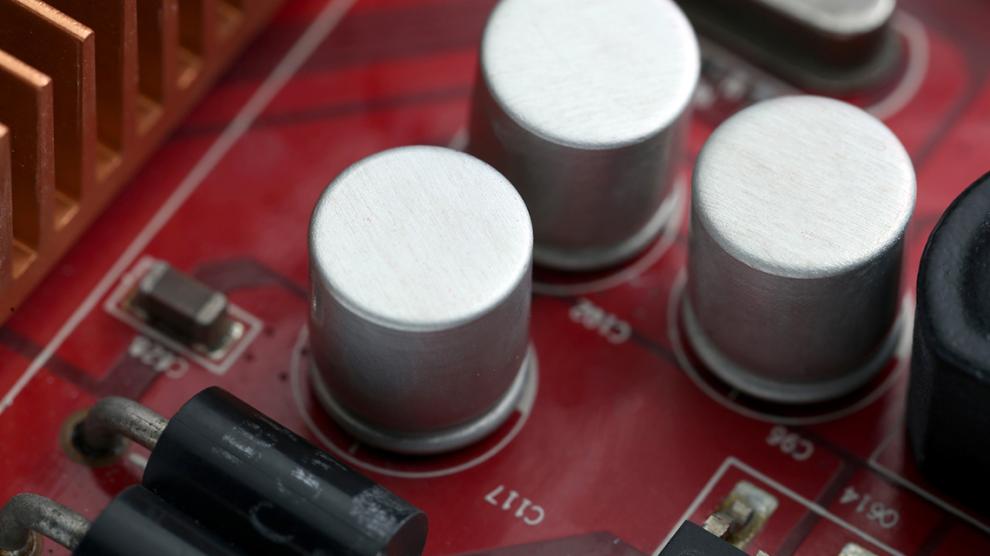
This milestone demonstrates the successful integration of a 1000V / 150 kW power converter, a modified electric machine, and a gearbox into a unified system architecture. The report offers an in-depth account of the engineering process, outlining both the technical challenges and the innovations that have shaped the development of the Integrated Motor Drive (IMD).
Modular Integration and Scalable Design
A key feature of the RHODaS prototype is its “3-in-1” modular design, which combines the motor, inverter, and gearbox within a compact assembly. This architecture optimises power density, mechanical simplicity, and cost efficiency, making it ideal for high-performance applications in commercial electric transport.
Although full housing-level integration was not achieved in this phase, the report includes a detailed 3D CAD model of the intended IMD configuration, providing a scalable blueprint for future iterations and enhancements. The modular approach ensures adaptability to evolving technologies and supports customisation for different vehicle platforms.
Advanced Thermal and Electrical Engineering
Thermal management was central to the design process. The electric motor features an innovative dual-channel cooling system, which independently regulates the stator and rotor temperatures—ensuring thermal stability under demanding conditions.
Similarly, the high-power inverter includes a heatsink design that improves cooling efficiency and supports the system's high power density. These strategies are reinforced by robust electrical components, including modular DC-link capacitors and silver-plated high-voltage terminals, which meet stringent automotive-grade standards.
Enhanced Usability and Control
Usability and operational reliability were also prioritised. A custom-designed Graphical User Interface (GUI) enables real-time control, parameter adjustment, mode selection, and fault diagnostics. This intuitive interface ensures safe and efficient operation under various environmental conditions, including high altitudes and elevated temperatures.
To support testing and system verification, the gearbox was fitted with additional sensors, enabling precise alignment and interaction with both the inverter and motor components.
Performance Metrics and Future Outlook
The RHODaS prototype achieves impressive results in power density:
- Volumetric density: 97.6 kW/l
- Gravimetric density: 28 kW/kg
These figures reflect significant progress toward meeting the high efficiency and compactness demands of the heavy-duty EV market. The report also outlines opportunities for further optimisation, such as the use of lightweight materials and custom-designed mechanical interfaces.
Next steps in the project will focus on:
- Validating efficiency profiles and protection strategies
- Exploring advanced materials
- Improving component modularity for easier maintenance and integration
Conclusion
This research highlights RHODaS’s commitment to technical excellence and sustainable innovation in electric propulsion systems. By overcoming integration challenges and implementing advanced thermal and electrical strategies, the project is establishing a strong technological foundation for the next generation of electric powertrains.
As RHODaS moves forward, the insights gained will continue to drive impactful developments in modular, scalable, and energy-efficient solutions for heavy-duty electric transport across Europe.